Mining Topic: Rock Dusting
What is the health and safety problem?
Accumulations of combustible dust in coal mines create the risk of large-scale explosions that can result in multiple deaths and traumatic injuries. The explosion hazard can be effectively controlled through the application and mixing of quality rock dust, such as limestone dust, to render inert the combustible coal dust generated during the mining and transport of coal. Recent studies have uncovered a number of concerns related to rock dusting. (1) How much rock dust is needed to effectively inert the coal dust? (2) How can researchers more efficiently and more effectively determine the potential explosibility of coal and rock dust mixtures? (3) Is the rock dust meeting the quality standards necessary to provide proper inerting? (4) How do mine operators keep the rock dust from caking and reducing its effectiveness?
What is the extent of the problem?
Rock dusting problems are universal to the coal industry and applicable to all operating underground bituminous coal mines. An explosion can propagate with as little as 0.01 inches of float coal dust on top of pure rock dust, suggesting the need to simultaneously apply rock dust as the mining face advances.
How is the NIOSH Mining program addressing this problem?
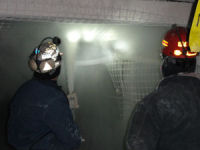
2 miners rock dusting a mine entry.
The NIOSH Mining Program has a comprehensive long-range research program to investigate problems related to the detection, prevention, and suppression of coal dust explosions. NIOSH researchers have conducted large-scale and laboratory-scale experiments to examine the influences of coal dust and rock dust particle size and concentrations needed for the prevention of coal dust explosions. Researchers have conducted extensive in-mine studies to determine the average size of coal dust particles found in intake airways that result from modern mining methods. These particles found in intake airways have been compared to the average coal particle size upon which the original 65% rock dust inerting requirement was based.
NIOSH researchers are investigating potential rock dust application and mitigation techniques to determine if respirable rock dust levels can be lessened. NIOSH researchers are also assessing and developing test methods by which companies can certify the rock dusts used in underground coal mines.
What are the significant findings?
Through large-scale testing, NIOSH researchers determined that 80% total incombustible content when mixed with coal was needed to prevent dust explosions in intake airways. The Coal Dust Explosibility Meter (CDEM) was developed and commercialized for use by mine operators and mine inspectors to assess the potential explosibility of a coal dust-rock dust mixture. The CDEM can be used by mine operators to manage their day-to-day rock dusting practices.
NIOSH also issued a Hazard ID on non-conforming rock dust to alert the industry that some rock dusts were not meeting the particle size and caking specifications set forth in MSHA regulations. NIOSH determined that rock dusts not conforming to these requirements were being used in U.S. underground coal mines. The use of non-conforming rock dust reduces the protection from potential dust explosions.
If rock dust absorbs moisture and forms a cake, it is unlikely to be scoured and entrained in the pressure front of an explosion, thus reducing the ability of the rock dust to inert the coal dust and prevent the explosion from propagating. Studies have identified the key factors that contribute to the caking properties of rock dust. NIOSH has worked with manufacturers to develop anti-caking rock dusts. The anti-caking treated rock dusts are as effective as non-treated rock dusts and may be most appropriate for application in areas of the mine where travel of personnel and equipment is infrequent, such as by seals and in tailgate entries. The enhanced fluidity of the rock dust when treated would enable better pneumatic transport of the rock dust. With resistance to water absorption, hard-to-reach areas by seals and in tailgate entries could be dusted with treated rock dust without the necessity of returning multiple times a year to re-dust in order to maintain rock dust dispersibility.
Federal law now requires that an incombustible content of 80% be maintained within 40 feet of the face, making wet rock dusting amenable to some operations to avoid respirable dust exposures. Wet rock dusting is performed by mixing rock dust with water and spraying it on the roof and ribs. However, once the wet mixture dries, the rock dust may cake, preventing it from being adequately dispersed to inert a propagating explosion. New technologies have emerged which employ a similar wet dusting technique where small amounts of additives are mixed into the rock dust and water slurry before spraying onto the exposed mine surfaces. The additives are to ensure that the resulting dry layer is able to be scoured by a pressure front. However, no required testing of these additives currently exists to determine if they function properly and if they are equivalent in behavior to a dry rock dust application. NIOSH designed a dust dispersion test method in which a reproducible pulse of air is applied to a bed of rock dust and the resulting dispersed dust cloud is assessed and compared to NIOSH’s reference rock dust performance. This test method can be used to evaluate the relative dispersibility of the sample.
The work in this topic area is supported by the NIOSH Mining Explosion Prevention program. See the NIOSH Mining Products page for software, guides, training materials or other items related to this topic.
Visit our Site Browser to see a search returning all pages tagged with Rock Dusting, including the Noteworthy Publications & Products listed below. Once there, you can continue to add or remove search terms to find the information you need.
- Coal Dust Explosibility
- Coal Dust Explosibility Meter Evaluation and Recommendations for Application
- Coal Dust Particle Size Survey of U.S. Mines
- Field Evaluation of the Coal Dust Explosibility Meter
- Funding Opportunities
- How Does Limestone Rock Dust Prevent Coal Dust Explosions in Coal Mines?
- How to use the Coal Dust Explosibility Meter
- Mitigating Coal Dust Explosions in Modern Underground Coal Mines
- NIOSH Hazard ID 16 - Non-Conforming Rock Dust
- Recommendations for a New Rock Dusting Standard to Prevent Coal Dust Explosions in Intake Airways
- Rock Dusting Considerations in Underground Coal Mines
- Technical Development of the Coal Dust Explosibility Meter
- Technology News 515 - Float Coal Dust Explosion Hazards