Research Rounds – Volume 3, Issue 12, June 2018
NIOSH Research Rounds is a monthly bulletin of selected research conducted by researchers at NIOSH and NIOSH-funded researchers at other institutions.
Volume 3, Number 12 (June 2018)
Inside NIOSH:
“Machine Learning” Targets Prevention of Musculoskeletal Injuries, and Slips, Trips, and Falls
Low back strains, carpal tunnel syndrome, and other soft-tissue musculoskeletal injuries are the most frequent causes of missed workdays in the United States, and most result from ergonomic, slip, trip, or fall hazards, according to the Bureau of Labor Statistics,. Fortunately, most of these hazards can be minimized through workplace interventions. One effective approach is ergonomics, which is the study of preventing musculoskeletal disorders through workplace design and policies.
The first step to designing ergonomic interventions is to identify workplaces that need them. In a paper published in the Journal of Occupational and Environmental Medicine, NIOSH researchers describe how they used computer programming—specifically, machine-learning—to identify industries at high risk for these prevalent hazards. Study lead author Alysha Meyers, Ph.D., NIOSH epidemiologist, explains the study and its results.
Q: What is unique about the study?
A: We applied machine learning to identify work-related injuries by cause, using workers’ compensation records for about two thirds of Ohio workers. Machine learning uses algorithms to “teach” a computer to perform a certain task. For example, in our study we applied a mathematical machine-learning technique to quickly and accurately code workers’ compensation claims into one of three groups: 1) ergonomic; 2) slips, trips, and falls; and 3) other.
Ultimately, the machine-learning technique enabled us to identify those industries and groups that face a greater risk of injury from ergonomic-related, slip, trip, or fall hazards. Identifying these high-risk industries tells us where we need to focus ergonomic or safety interventions.
Q: What did you find?
A: Workers in Ohio skilled nursing facilities were at the highest risk for severe (more than 7 missed workdays) ergonomic-related claims, and workers in the general freight trucking industry are at the highest risk for severe slip, trip, or fall claims.
Using data from the Ohio Bureau of Workers’ Compensation, we analyzed more than 1.2 million claims from 2001 to 2011 representing more than 200 industries. We then ranked these claims for musculoskeletal injuries that could have been prevented with workplace interventions to prevent ergonomic-related injuries, or slips, trips, and falls.
Q: What are the next steps?
A: Already, our findings are helping occupational safety and health specialists to focus their injury prevention efforts on high-risk occupations and industries. This activity is especially apparent in Ohio, where our study took place, but researchers in other states could use our study to develop similar approaches.
More information is available:
- Applying Machine Learning to Workers’ Compensation Data to Identify Industry-Specific Ergonomic and Safety Prevention Priorities: 2001 to 2011
- NIOSH: Ergonomics and Musculoskeletal Disorders
- NIOSH: Slip, Trip, and Fall Prevention for Healthcare Workers
- NIOSH: Center for Workers’ Compensation Studies
- John Howard, M.D., Director
- Christina Spring, Editor in Chief
- Anne Blank, Story Editor
- Cheryl Hamilton, Copy Editor
- Glenn Doyle, Technical Lead
- Tonya White, Technical Support
Lift-assist System Has Baggage Handlers’ Backs
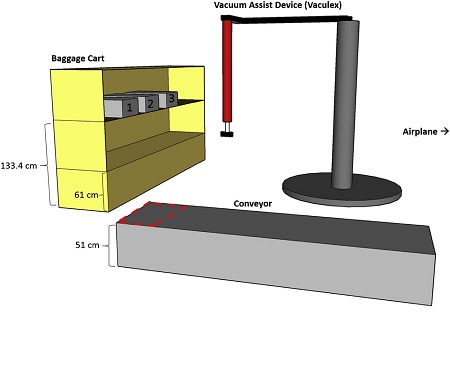
For travelers, restrictions on baggage weight may mean packing fewer pairs of shoes. For airport baggage handlers, weight restrictions, combined with proper lifting, are important to safety and health but may not be enough to prevent work-related back injuries.
Compared to other occupations, baggage handling has the third-highest rate of musculoskeletal injury, according to the most recent figures from the Bureau of Labor Statistics. Previous studies show that most of these injuries involve the back. One way to prevent back injury is by using mechanized lift-assist systems, but little information is available about their effectiveness in reducing biomechanical risks of back injury among baggage handlers.
To look at the issue, a NIOSH investigator and researchers from the Ohio State University tested a vacuum lift-assist system in the laboratory and simulated baggage-handling tasks similar to those that typically occur in the ramp area of an airport. Study participants included eight males and two females with an average age of 26. They lifted baggage that weighed 14.5 kilograms (31 pounds), the average for travelers’ checked-in baggage, from a conveyor belt to a two-shelved baggage cart and back. Using a special research technique to record the electrical activity levels of many back muscle groups during lifting, the investigators estimated the level of compressive and shear forces acting on the spine. They compared the effects of manual lifting to the effects of lifting with a commercial lift-assist system, which has the capacity of lifting a load up to 50 kilograms (110 pounds).
The study found that the lift-assist system significantly decreased the amount of spinal loads to workers’ backs when lifting baggage. Specifically, it decreased compressive forces (i.e., top down force compressing on the spine) on the lower back by 39%, and the shear force (i.e., lateral force from the front to the back) on the spine by 25%, according to the study published in the journal Applied Ergonomics. In addition, the study found that the greatest back strain occurred when lifting baggage to the top shelf of a baggage cart. These findings show that lift-assist systems could help prevent back injury among baggage handlers, particularly when loading baggage to these top shelves.
More information is available:
Outside NIOSH:
Study Aims to Improve the Health of New Construction Workers
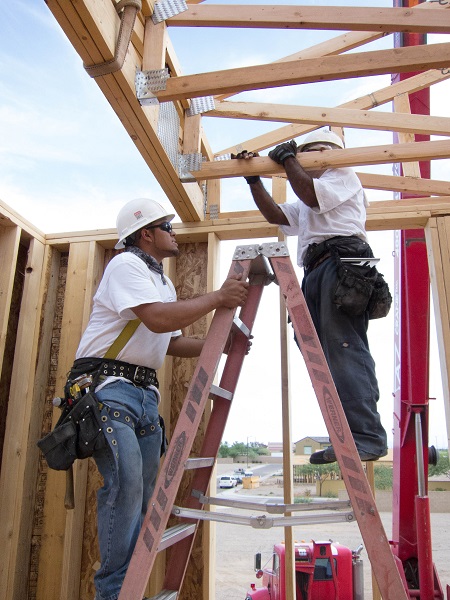
With spring’s warmer temperatures, many workers may be heading off to new jobs in construction. As one of the most dangerous occupations in the United States, construction poses the greatest safety and health risks to new workers, according to the Bureau of Labor Statistics.
In addition to the hazards of working at heights and with heavy equipment and chemicals, often amid clouds of dust, construction work can present other, less visible hazards that extend beyond the workplace. These hazards include irregular and long hours, lengthy commutes to different job sites, and extended workdays. In turn, these hazards can increase the risk of psychological stress among workers and, subsequently, risky health behaviors, including poor nutrition and substance abuse.
An ongoing NIOSH-funded study at the University of Iowa in Iowa City, in partnership with Washington University in St. Louis, is taking a holistic approach to worker health to minimize these risks. Although we often think of workplace safety and health as being confined to the worksite, the Total Worker Health® (TWH) approach views the conditions of work and the worker both in and out of the workplace. Consistent with traditional occupational safety and health prevention principles, the TWH approach recognizes that job-related factors can have an important impact on the well-being of workers, their families, and their communities. Issues such as wages, work hours, workload and stress, workplace interactions, access to paid leave, healthy workplaces, and safe worksites can be addressed through organizational programs, policies, and practices.
Currently in its 2nd year, the 5-year study is looking at the health-related behavior of new workers in three construction trades: carpentry, floor-laying, and boilermaking. Ultimately, the study aims to identify effective ways to change these behaviors to decrease the risk of work-related illness and injury. Investigators are working with a local carpenters’ council and an international construction workers’ group. The study’s aims are to 1) evaluate the effects of work on the health behaviors of new carpenters, floor-layers, and boilermakers; 2) identify current workplace health programs in these trades; and 3) determine the feasibility of working with unions, insurance companies, and other groups to improve the health and well-being of new construction workers.
To date, investigators have surveyed 912 carpenters, floor-layers, and boilermakers about work and health behaviors. In addition, they completed two focus groups with general contractors, subcontractors, and union representatives and interviewed a potential partner for implementing safety and health interventions. Final results are expected when the study concludes in 2021.
More information is available:
- Impacting the Safety, Health, and Well-being of Construction Apprentices
- NIOSH: Total Worker Health®
- NIOSH: Construction Safety and Health
- NIOSH Centers of Excellence for Total Worker Health®
Pilot Study Connects Employers to Create Family-Friendly Workplaces
As most working parents know, finding the right work-life balance can be tricky. Music recitals, sports practices and games, field trips, doctor appointments, homemade family dinners, and … a 40-hour (or, in some cases, more) work week?
Fortunately for working families with young children in Colorado, a NIOSH-funded center at the Colorado School of Public Health is investigating ways to help. The Family Friendly Workplace Initiative, a community-based public health partnership, aims to connect businesses and other organizations throughout the state to implement family-friendly policies and strategies that work for working parents. Taking a novel two-pronged approach, the initiative collects and analyzes information about current family-friendly policies and programs while simultaneously providing the resulting information to employers who want to improve their own workplaces.
Already, investigators have gathered information from more than 50 organizations in Colorado, representing nearly 72,000 employees, about their efforts to provide family-friendly workplaces. They have also used focus groups to ask employers about their efforts to support work-life integration. Preliminary results suggest that employers taking the assessment are motivated to adopt family-friendly practices. Specifically, 96% provided accommodations for nursing mothers, 62% had a written policy for flex-time, and 84% offered a form of paid family medical leave. Organizations cited improving morale (91%) and retention (84%) most frequently as the reasons they offer family-friendly benefits. The information will help investigators identify best practices for adoption and implementation of Family-Friendly policies to improve worker well-being across small and large organizations from various industries.
Employers interested in participating can visit the Family Friendly Colorado webpage to access the Family-Friendly Assessment and comprehensive employer toolkit. The assessment helps organizations measure the family friendliness of their workplace, identify areas for improvement, and receive recognition for their efforts. The assessment includes questions in four areas that are critical to creating a family-friendly workplace: benefits and leave; flexibility; new parents; and communication, education and training. In addition to practical steps for supporting policies and programs such as accessible child care, the toolkit provides case studies from organizations with effective family-friendly programs already in place. Family-Friendly Colorado plans to expand the program to offer the Family-Friendly Assessment to more employers this upcoming year.
More information is available:
- Center for Health, Work & Environment, Colorado School of Public Health
- Family Friendly Colorado
- NIOSH Centers of Excellence for Total Worker Health®
- NIOSH: Total Worker Health®
Mention of any company or product does not constitute endorsement by NIOSH.