Research Rounds – Volume 4, Issue 3, September 2018
NIOSH Research Rounds is a monthly bulletin of selected research conducted by researchers at NIOSH and NIOSH-funded researchers at other institutions.
Volume 4, Number 3 (September 2018)
Inside NIOSH:
Controlled Fire Study Finds High Levels of Airborne Chemicals
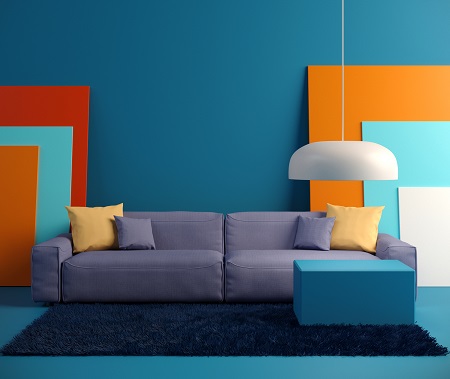
What do plastic, polyester, and foam have in common? They are synthetic materials found throughout most modern homes in everything from toys to furniture to appliances. Unlike wood, cotton, and other natural materials, synthetic materials are made in laboratories through chemical processes.
During a fire, these chemicals can burn hotter and faster, and produce more toxic smoke than natural materials. Evidence suggests that work-related exposure to these toxicants among firefighters corresponds to an increased risk of acute cardiovascular events and cancer.
To understand the risk of exposure from residential firefighting, NIOSH investigators and university and industry partners measured hazardous air emissions during different stages of firefighting. The investigators set 12 separate fires in safe and controlled settings to simulate residential firefighting conditions. This included furnishing the structures with modern fixtures. Six of the fires involved firefighters entering through the front door of the building to extinguish the fire. The others involved firefighters first dousing the fire through a bedroom window before entering through the front door.
Investigators then collected air samples for several chemicals, including benzene and other volatile organic compounds, poly-cyclic aromatic hydrocarbons, and hydrogen cyanide. For comparison, they tested air from three areas: 1) inside the structure during active fire; 2) inside the structure after fire suppression, also known as overhaul, when firefighters search for and extinguish any smoldering items; and 3) outside the structure near exterior crew-members like the incident commander. In addition, they took personal air measurements associated with job types in all three areas: fire attack, victim search, overhaul, outside ventilation (help vent smoke from structure), and command/pump operator tasks.
- John Howard, M.D., Director
- Christina Spring, Editor in Chief
- Anne Blank, Story Editor
- Cheryl Hamilton, Copy Editor
- Glenn Doyle, Technical Lead
- Tonya White, Technical Support
In general, median personal air measurements collected from interior crew-members were substantially higher than the recommended exposure limits for short-term exposure for the chemicals measured. Significant differences occurred by job type, with search and attack exhibiting the highest levels of chemical exposure. The maximum levels recorded for hydrogen cyanide for firefighters assigned to attack, search, and outside ventilation were higher than levels considered immediately dangerous to life and health. Outside ventilation crews may not always wear respiratory protection and as a result could breathe in the chemicals that were measured. Even though search and attack firefighters wear self-contained breathing apparatus to protect their lungs, exposure could also occur via the skin, either through direct contact or when removing contaminated gear after the fire.
Area air measurements also showed that the median amount of several chemicals tested was higher than recommended short-term exposure limits. Even in the area outside the burning structure, where workers like the incident commander typically do not wear respiratory protection, area air measurements downwind of the fire were higher than naturally occurring levels. These results highlight the importance of wearing self-contained breathing apparatus, even when firefighters are assigned to post-fire suppression jobs or exterior operations. They also show the need for establishing command centers upwind of a fire or, if that is impossible, wearing self-contained breathing apparatus for protection against airborne chemicals, according to the study published in the Journal of Occupational and Environmental Hygiene.
More information is available:
Exposure to Flame Retardants in Foam Found among Gymnastics Coaches
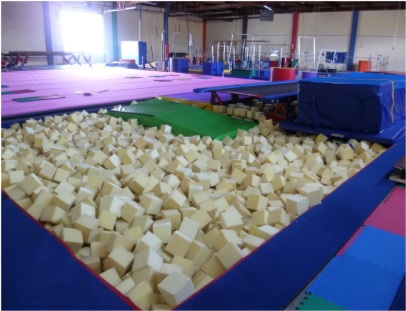
To protect gymnasts from injury during training, polyurethane foam provides padding in the form of loose blocks, mats, and other equipment. To prevent the spread of fire, this foam also may contain flame retardants, potentially hazardous chemicals that could cause health problems for both gymnasts and coaches.
In 2004, the United States banned the use of one class of these flame retardants, PBDE, or polybrominated diphenyl ethers, following reports of links to hormonal disruption and increased risk of cancer. Since then, other flame retardants have taken their place in many products, including foam. The potential harmful effects of these new flame retardants are unclear, but some studies indicate that they, like their banned predecessors, also could disrupt the hormonal system and increase cancer risk. But questions exist: Does work-related exposure occur, and if so, by which route? Does cleaning or removing a source prevent exposure?
To answer these questions, NIOSH investigators measured gymnastic coaches’ exposure to 22 flame retardants in four gymnastics studios, at the request of the owner who expressed concern about foam blocks. First, investigators showed coaches how to wipe their hands using hand wipes. After the coaches wiped their hands, investigators sent the wipes to a laboratory for testing. Investigators collected the hand wipe samples before and after the gymnastics studios cleaned their facilities and replaced old foam blocks with new ones labeled as free of PBDEs and other flame retardants.
The investigators collected hand wipes from 20 coaches before the foam was replaced and from 18 coaches after the foam was replaced. Hand wipes were collected at the beginning and end of one shift. To look at how flame retardants might be distributed in dust deposits on windows, investigators wiped window surfaces, both inside the gyms and in other areas such as offices. Finally, they measured the levels of flame retardants in both the old and new replacement foam blocks.
When compared with the wipes taken before a work shift, post-work hand wipes showed significantly greater levels of 9 out of 13 flame retardants measured, according to the paper published in the journal Environment International. However, these across-shift increases were smaller after the studios cleaned the gymnastics studios and replaced the foam blocks with blocks certified as PBDE-free.
Measurements of 3 of the 13 flame retardants were significantly higher on windows in the gymnastics areas as compared with those in other areas, suggesting the potential for airborne exposure. The three highest levels of flame retardants found on gymnastics area windows were also found in the old foam blocks. Although the study found no PBDEs in the new blocks, it did find several other common flame retardants, highlighting the challenges of identifying chemicals in new products.
The health effects associated with flame retardant exposures are not yet well understood. While research on the potential health effects is being done, the authors recommended ways that employees and employers can minimize gymnastics coaches’ airborne and skin exposure to flame retardant:
- Review the foam safety data sheet information or contact the manufacturer about flame retardant content before purchasing new foam equipment, even if the foam is certified as flame-retardant free.
- Purchase new foam products that contain little or no flame retardants.
- Improve housekeeping practices, including using personal protective equipment during cleaning.
The study took place in 2014 and 2015 as part of the NIOSH Health Hazard Evaluation program. This free program, available upon request, provides information about possible work-related health hazards to workers, employers, and unions.
More information is available:
- Occupational Exposure to Polybrominated Diphenyl Ethers (PBDEs) and Other Flame Retardant Foam Additives at Gymnastics Studios: Before, During and After the Replacement of Pit Foam with PBDE-free Foams
- NIOSH Pocket Guide to Chemical Hazards: Bromine
- NIOSH Health Hazard Evaluation
Outside NIOSH:
Many employers now offer programs to help improve workers’ safety and health, as well as morale and productivity. At NIOSH, the Total Worker Health® Program supports research on these programs and the myriad of factors, both inside and outside of the workplace that affect workers’ overall safety, health, and well-being. The following articles describe two NIOSH-funded studies aimed at improving the implementation and evaluation of different workplace safety and health programs.
Job Design Linked to Participation in Workplace Wellness Programs
Workplace wellness programs often offer an array of health-improvement activities, including courses to quit smoking, exercise or physical fitness classes, nutrition or stress management education, and ergonomic testing of work conditions and equipment. In 2017, 39% of private industry workers and 63% of state and local government workers had access to such programs, according to the Bureau of Labor Statistics. However, access does not always mean that employees use these programs.
To understand obstacles to use, NIOSH-funded researchers at the University of Massachusetts Lowell and the University of Connecticut explored six different factors. These included job demand, job control, social interactions, leadership, role expectations, and predictability at work. They used surveys, interviews, and focus groups to identify which factors affected participation in workplace wellness programs among 343 employees at a public university in New York.
Of the six factors, job control was the most likely to improve participation in workplace wellness programs, followed by social interactions and then job demand, according to the study published in the Journal of Workplace Behavioral Health. Job control refers to the freedom to choose when and how to complete work. This can include providing flexibility to make time for doctor’s appointments, exercising, or meeting with a nutritionist without worrying about work schedules. Social interactions include support from coworkers and management, which reflects employees’ satisfaction with their relationship with their supervisors. This supervisor-employee relationship was found to play a critical role in employee participation in workplace wellness programs.
Job demand is defined as the worker’s perception of the job’s physical and mental demands. Study participants with either low or high levels of job demand reported increased participation in workplace wellness programs. Researchers found that workers with increased job demands participated in these programs to relieve stress.
These findings suggest that successful workplace wellness programs should also address the way jobs are designed to remove any barriers to participation, especially offering flexible work hours and supervisory support.
More information is available:
- Interactive Effects of Work Psychosocial Factors on Participation in Workplace Wellness Programs
- Workplace Psychosocial Environment and Employees’ Health Behavior: More Evidence to Support the Link
- NIOSH Total Worker Health® Program
- NIOSH Extramural Research and Training Programs: NIOSH Centers of Excellence for Total Worker Health®
- Center for the Promotion of Health in the New England Workplace
New Tool Measures Effectiveness of Workplace Safety and Health Programs
As more organizations offer increasingly comprehensive programs for workplace safety and health, researchers and organizations alike look for the best examples and tools to measure their effectiveness. With so many programs available, how do organizations know which one is best?
Through a NIOSH-funded study at the Harvard T.H. Chan School of Public Health, scientists designed a new tool to help, according to research published in the Journal of Occupational and Environmental Medicine. The Workplace Integrated Safety and Health (WISH) Assessment measures policies, programs, and practices that promote worker safety, health, and well-being.
The WISH Assessment is an expansion of a previous measurement tool, developed by the same researchers in this study. The scientists created this latest assessment tool based on an extensive review of published literature on workplace wellness programs, repeated cognitive testing, and semi-structured interviews. They tested and revised the WISH Assessment to ensure that its elements were clearly understood and effectively measured the intended concepts.
The researchers finalized the tool after identifying six factors for protecting and promoting worker safety, health, and well-being: 1) leadership commitment; 2) participation; 3) policies, programs, and practices that foster supportive working conditions; 4) comprehensive and collaborative strategies; 5) adherence to federal and state regulations and ethical norms; and 6) regular evaluations that guide safety, health, and well-being activities.
Next steps include additional testing on the WISH Assessment to validate the tool across multiple samples, and designing and testing a scoring system that organizations can use. Harvard researchers plan to use the WISH Assessment in a future study focused on the association between Total Worker Health® approaches and quality-of-care outcomes in 500 nursing homes. Ultimately, the WISH Assessment could help direct priorities among organizations, guiding research in workplace policies, programs, and practices to improve worker well-being.
More information is available:
- Measuring Best Practices for Workplace Safety, Health, and Well-Being: The Workplace Integrated Safety and Health Assessment
- NIOSH Total Worker Health® Program
- NIOSH Extramural Research and Training Programs: NIOSH Centers of Excellence for Total Worker Health®
- Harvard T.H. Chan School of Public Health Center for Work, Health, & Well-being
Mention of any company or product does not constitute endorsement by NIOSH.